Case study
Enterprises, mid-sized businesses, and small retailers need a way to organize, handle, and store their products, as well as balance demand and supply. That’s where warehouse management comes in. It helps you meet customer demands and ensure on-time delivery by tracking picking, packing, stowing, and delivery. Warehouse management can significantly reduce order lead times, inventory turnover, and return rates, especially with warehouse management systems (WMS). Standalone or embedded in ERP, WMS can enhance inventory visibility, reduce mispicks, and cut operating costs. Our blog post gives you a few tips on choosing the right solution.
No matter if you have a sufficient amount of inventory to fill numerous football stadiums or hardly enough to fill your small garage, the appropriate management of your products’ journey is critical for the e-Commerce and retail industry to succeed. Today, customers want to receive the ordered goods in the selected specifications much quicker than ever before.
Guide to warehouse management
Although it may sound simple, how can you ensure the relevance of your inventory list and
determine whether it matches the available stock on the shelves of your warehouse right
now? How can you check whether the refrigerated products are packaged properly for
shipping before the delivery drivers load these items, so they are not spoiled?
Starting from product purchase to its final delivery, we have collected the best possible practices
and valuable insights, along with warehouse management software recommendations, that can be
suitable for product companies of different sizes, including even small and medium-sized ones.
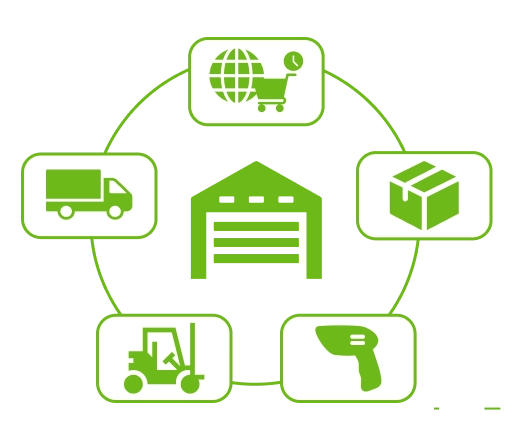
Warehouse management is the process that involves receiving, storing, stocking, and protecting products and items while they wait for shipping to their final destination. It means that warehouse management plays a crucial role for organizations that sell physical goods. Investing in trucking app development can significantly enhance the efficiency of warehouse operations by optimizing delivery schedules and inventory management. Warehouse management covers seven various stages in supply chain logistics and functions as the origin point for last-mile delivery. Thus, the productivity of your warehouse staff can determine how fast your clients get the ordered goods. One of the prominent warehouse management features is that it is always connected with the warehouse employees who perform their work in a relevant warehouse and carry out multiple day-to-day operations of the supply chain management scm process. To better understand what is warehouse management, we should define what warehouse means, name the key types of warehouse, and analyze the main principles, benefits, and challenges related to warehouse management.
What is a warehouse?
The warehouse is a storage facility that provides necessary space and robotics instruments
to handle products, along with storage racks and human staff for managing the inbound and
outbound goods. All these things and other multiple small additions allow a warehouse to
work properly. In other words, this storage facility functions within a warehouse
management system and serves as a critical part of not only warehouse management but also
supply chain logistics.
What about the main types of warehouse – they are classified depending on their application:
- Retail warehouse - the particular stores deal with consumer goods and are located in single-level buildings;
- Cold storage - these facilities store temperature-sensitive goods used for different edible and non-edible products;
- Distribution and fulfillment warehouse - the manufacturers use such intermediary storage facilities for unloading products for distributors to deliver them to retailers;
- Hazmat (hazardous materials) warehouse - they provide safe storage of chemicals and other physically dangerous substances.
Principles of warehouse management
Understanding the general warehouse management principles allows focusing your efforts on optimizing the way your warehouse performs. The main principles are following:
- Know your purpose. Each warehouse operation needs to know its goals first.
- Comprehensive control. Warehouse management requires you to coordinate complex processes that include many moving parts such as equipment, orders, inventory, or employees.
- Flexibility and resilience. In the case of necessity, warehouse managers must be able to change plans immediately; for example, when you get the materials damaged or the inclement weather provokes delays in shipments.
- Customer orientation. On-time delivery, along with the right product, is among the most critical metrics to assess customer service and satisfaction.
- Data-driven decision-making. An appropriate warehouse management system allows pinpointing and analyzing areas to improve.
Benefits of warehouse management
The main purpose of warehouse management is to bring on-time delivery to customers. To achieve this goal, efficient warehouse management makes all warehouse processes running as accurately and effectively as possible. In this case, the main benefits of warehouse management are the next ones:
- Warehouse space optimization and inventory storage maximization;
- The inventory is easy for warehouse employees to find;
- The adequate warehouse staffing;
- The efficient order fulfillment;
- The appropriate cooperation with suppliers and transportation partners.
In other words, the mentioned benefits of warehouse management are significantly connected with providing high-quality service at a low cost. They can cover the entire supply chain logistics, improving relationships with suppliers and clients.
Challenges of warehouse management
All of the major challenges of warehouse management can relate to software or outsourcing, or even both. Thus, these challenges include:
- Material handling - all warehouse employees need to handle packages carefully;
- Space - one of the most critical warehouse management challenges, especially for small-sized companies since finding enough space for storing items can become a difficult task;
- Processing efficiency - each aspect of warehouse management (as well as of last-mile delivery) must be organized and streamlined to provide maximum possible efficiency;
- Customer experience - ultimately, the success of any organization depends on satisfying customer needs and meeting customer demands.
Type of warehouse management
Warehouse management serves as the process to administer and control the operations in the
warehouse space and synchronize it with the whole supply chain.
Nowadays, lean warehouse management methods are leading among the types of warehouse management
thanks to apparent business advantages because they generate more profits and require fewer
investments. In other words, the main idea of lean warehouse management involves adding value
with no need to add the burden of inventory management.
Firstly, lean warehouse management focuses on the assessment of cost centers within the warehouse
space for identifying the inefficiencies and curbing them. It starts with the warehouse layout,
which ensures that you keep the fast-moving SKUs close to the ground level.
Then, the racks are arranged for minimizing the wastage of warehouse space. The lean warehouse
management process recognizes inventory handling among the most critical inventory management
areas to optimize. Many technological tools, including barcodes, RFID tags, or even robotics,
aid these workhouse processes. You can control them centrally by using inventory management
software.
The next step to create a lean ecosystem requires minimizing the movement of products, along
with instances where employees touch them. That is because it can provoke the proliferation
and misplacement of the goods. Besides, among the actual advantages of lean warehouse management
is saving time. The ability to meet tight deadlines, ensure smooth operations in times of peak
demands, and ensure timely delivery of goods with no mistakes serves as an asset in the modern
market.
Thus, lean inventory and warehouse management is a holistic approach to improvising the output.
Warehouse management processes
Warehouse management is among the critical aspects of supply chain management that impacts order fulfillment, packing and shipping, inventory management, and the entire logistics management. Thanks to efficient warehouse management software, you can see what is happening in various warehouse locations in real-time.
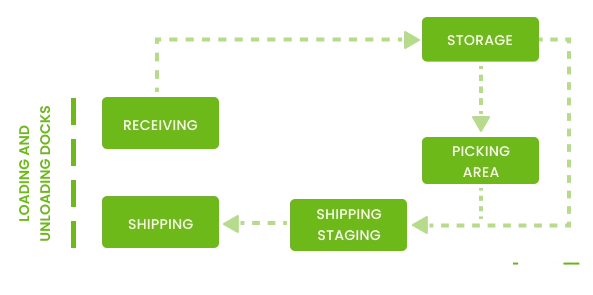
Inventory tracking
Inventory tracking means monitoring stock levels in the warehouse. That allows knowing
which SKUs you have, along with the exact locations where you store them or determining
whether they are on their way from manufacturers or to stores.
With the appropriate inventory management software, warehouse managers can define the number
of items ready for shipping if a client ordered a product now and when you need to order more,
depending on projected volume.
As your company grows, the inventory management system will be helpful for turning inventory
over much quicker, expanding into new locations, and increasing product lines. That makes inventory
tracking more important for effective warehouse management.
Picking and packing
Picking and packing serve as two fundamental functions to perform in the warehouse.
Warehouse management systems must generate relevant pick lists for all pickers to retrieve
products most effectively. That can involve zone, wave, or batch picking.
If the new order appears, the picker receives a relevant packing slip of the products ordered
and their storage locations in the facility. Then, the picker will collect these items from
their respective locations.
After picking the order, the picker hands it off to the packer. The last one must place the
products in a box safely, add in necessary packing materials, and put a shipping label.
Receiving and stowing
Each warehouse operation must have special loading docks that allow receiving inventory
from trucks. After receiving, you must stow the inventory away in a facility. With the
help of your warehouse management system, you should scan all new boxes received.
Then, you will bring the inventory to the respective short-term or long-term storage locations,
where you will scan it again. You can use inventory management systems to provide clear instructions
for all users, which allows them to learn the ways of receiving, unpacking, retrieving, picking,
packing, and shipping inventory.
Shipping
Depending on the delivery options or shipping services you provide your customers with,
various shipping carriers will pick up ordered items from your warehouse and deliver them
to the next destination.
After shipping the order, your warehouse management system must automatically send the required
e-Commerce order tracking data back to the store. That allows customers to track their orders.
Reporting
Thanks to warehouse management systems, you can provide your warehouse staff with
operational and inventory reports. That can involve accuracy in fulfilling orders, the
total number of orders fulfilled per hour, orders shipped on time, etc.
Besides, there can be reports regarding the employees’ operations, such as inventory forecasting,
for understanding labor management and requirements better. Using a specific warehouse management
tracking system, you may quickly define the employees with completed safety training or different
licenses and certifications.
Calculating warehouse performance
For business owners, a warehouse serves as an asset, which means it is critical to manage and calculate the rate of return. Thus, warehouse performance can be considered the warehouse’s confirmation regarding expected financial and operational indicators.
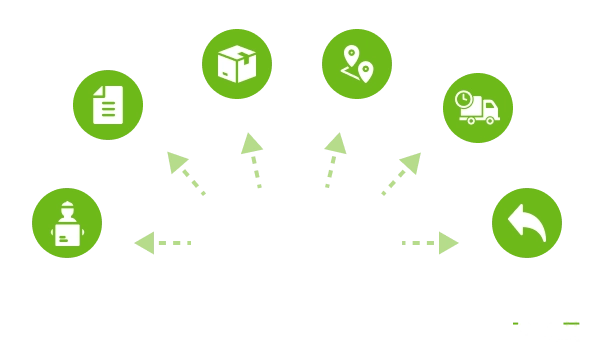
Order lead time
Once your company places the order, the total time needed to fulfill it and reach your premises is called the order lead time. This benchmark is critical for order management since the reorder levels depend on the lead time and a safety factor.
Inventory carrying costs
For each company, the unsold items hold the capital with no generating appreciation and lead to the carrying costs. That includes the facility’s rent, different utility services, and employees. The particular benchmark gives an understanding of how long the warehouse inventory must stay and the relevant addition to selling costs.
Inventory turnover
In the case of manufacturing, the inventory turnover proportion serves as the average time
required to turn raw materials into finished goods. But for online and offline retailers,
it is the number of times when they sell or purchase the inventory. This rate also
corresponds to the effective use of resources. If the turnover is high enough, the
financial health of the organization, including its order management, inventory
management, and supply chain, is also on the appropriate level. In our
tax management system project, we implemented solutions that streamlined financial tracking and optimized resource
allocation, leading to measurable improvements in efficiency.
To reach this goal, such metrics provide an understanding of any inefficiencies in management
solutions and help improve warehouse operations.
Rate of returns
This warehouse operation benchmark is the percentage return on the investments made by a company. That involves tangible and intangible investments the organization uses to create value. You can also count the rate of returns for each item individually to obtain an overview of all profitable investments.
Perfect order rate
Perfect order rate is considered the number of orders the company fulfills with no damage
during the order management process and with no mistakes on time against the total number
of orders. This index is one of the most powerful key performance indicators used to
measure efficiency because it emphasizes the increase in capital’s effective utilization
and customer satisfaction.
In addition, perfect order rate focuses on eliminating numerous shortcomings, including the
inventory shortage, the inappropriate performance of accounting software, or faulty handling.
If this rate is high, it can improve the company’s profitability and give insights regarding
the existing problem areas in warehouse operations.
Picking and shipping per hour
After confirming the orders, employees at the warehouse must pick the items from their
relevant locations. Picking can become hard in the case of product bundling or when the
warehouse layout is multi-storeyed. You can reduce the average time to pick products by
collecting them in batches. Besides, the employees should pay attention to the size of the
product to ensure optimal collection.
During the picking stage, you can also cut down shipping time per product by coordinating the
multi-product consignments. Meanwhile, using appropriate shipping stations also allows increasing
the average shipping time per item. High picking and shipping per hour server as benchmarks
of a significant warehouse management process.
Warehouse management fulfillment strategies
Selecting the appropriate warehouse management fulfillment strategies that can match your
company’s size and the number and type of received orders will allow shipping products
faster, minimizing waste, and improving customer satisfaction.
Implementing picking strategies that correspond to the type of orders your business receives
can help maintain an efficient warehouse management process.
For instance:
- Batch picking serves as a technique that allows fulfilling numerous orders for the same item quickly with no wasting time thanks to constantly revisiting the relevant storage location.
- Zone picking allows assigning pickers to various zones of SKUs. It means that for all orders, pickers are obliged to pick all SKUs from their assigned zones.
- First expired, first out (FEFO) picking is critical for ensuring that perishable products or items are delivered to customers before the expiration or sell-by dates. Applying this strategy in warehouse management processes requires the products and items that expire first to be shipped first.
- First in, first out (FIFO) picking helps ensure the first products and items that come into the warehouse will be the first for distribution. This strategy means that all older products and items will be shipped before becoming obsolete.
At the same time, technology also serves as a crucial part of all warehouse management fulfillment strategies.Using different handheld mobile devices which can display packing lists with product locations and their serial numbers helps improve picking speed, along with its accuracy. The efficient software can ensure cost-effective packing depending on product dimensions, which makes all items get shipped safely with minimal possible wasted space.
Best practices for warehouse management
What we have analyzed previously has been the core of warehouse management and the
warehouse management system. But you must remember that your objective during all the
stages of supply chain management is to satisfy your customers. For doing that, all
components of your warehouse management should be swift, effective, and optimized.
To meet your clients’ demands regarding the speed and flexibility of their orders and returns,
there is a need to apply warehouse management best practices, along with specific technologies
within your organization.
Below we provide a list of best practices for warehouse to implement for obtaining efficiency:
Automating time-consuming warehouse operations
To reduce order processing time and relevant costs, you need to think about using automation bots during the dispatch process. Thanks to applying these bots for speeding up the order processing, the employees at the warehouse will focus on more critical things such as picking and packing and shipping items quickly. That helps improve customer satisfaction and leads to more sales.
Using barcodes and barcode scanners
Implementing Bluetooth barcode scanners helps warehouse staff with picking and packing processes. That also allows eliminating potential human errors related to mistyping numbers. Thus, using this particular technology can significantly enhance your perfect order rate, reduce costs and processing times, which results in more efficient logistics management.
Implementing EDI integrations
EDI (electronic data interchange) means the computer-to-computer exchange of various files
between two parties like business partners using a standard electronic format. This
approach is becoming popular among the best practices for warehouse management and is
suitable for companies of all sizes.
By applying EDI, your business can:
- Prevent double selling;
- Cut down the number of incorrect shipping documents;
- Reduce the amount of missed delivery deadlines;
- Provide better control over supplier delays;
- Send tracking data to clients automatically.
- Applying an integrated warehouse management system
Warehouse management statistics show that 43% of US companies continue to use pen and
paper in their warehouse management. Just imagine the amount of time warehouse employees
spend to check inventory, write figures, and update systems manually after that.
However, applying an integrated warehouse management system allows easily scanning items within
the warehouse, checking and updating inventory levels, prioritizing picking lists, and performing
inventory counts quickly with the help of accounting software.
Analyzing the warehouse efficiency frequently
The ability to make your warehouse run smoothly is one of the key business priorities, especially when you deal with the increasing number of your warehouses, sales growth, or faster turnaround times required by customers. Thus, getting the correct and frequent reports is critical to access different processes within the warehouse, including stocking, pulling, or inventory management.
Warehouse management system
A warehouse management system (WMS)
serves as software created for optimizing the warehouse management, distribution process, supply
chain, and order fulfillment within a company.
Traditionally, a WMS provides the functionality necessary for streamlining and improving all
warehouse processes, from the moment when product and items first enter the facility, through
the further putaway process, and to the moment they leave the warehouse (and even in the case
of their return).
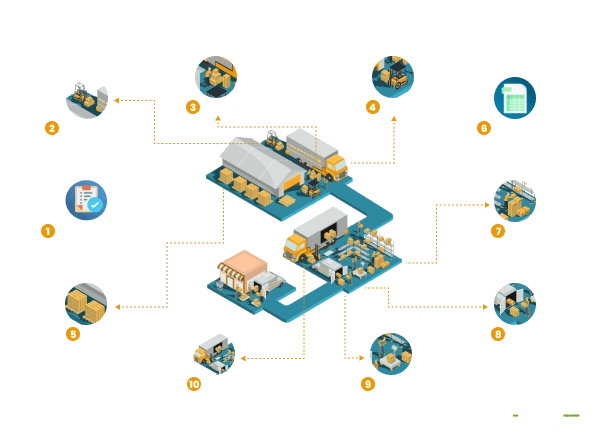
Modern warehouse management systems can be integrated with other different types of software, which allows making all warehouse operations interconnected, smooth, and streamlined. Thus, a WMS is something that corresponds ideally to the existing omnichannel retail, which is crucial for conducting efficient warehouse management and meeting customer demand.
Types of warehouse management systems
After learning the fundamentals of a WMS, you can start considering the types of warehouse
management systems that will be suitable for your organization.
There are two main types of warehouse management software.
The first option is selecting a standalone product and then integrating it with the rest of
your company’s back office and other operational systems. Meanwhile, the second option is selecting
an integrated solution that allows the WMS to share the same database and workflows as provided
by your order management, inventory, and accounting software.
Thus, a standalone WMS belongs to the specialized types of warehouse management software. The
focus of this WMS is on warehouse management features, even though you can integrate it with
other software that deals with inventory control and order management.
On the other hand, an integrated WMS serves as a solution that you can include in your current
ERP or back-office software or as an additional module you can purchase from a back office
or ERP vendor.
Benefits of warehouse management system
There can be multiple benefits of a wms for your organization, from bringing to it the
ability to make quick data-driven decisions, to decreasing processing costs, along with
order fulfillment latency.
Here we describe the top-5 benefits of warehouse management system:
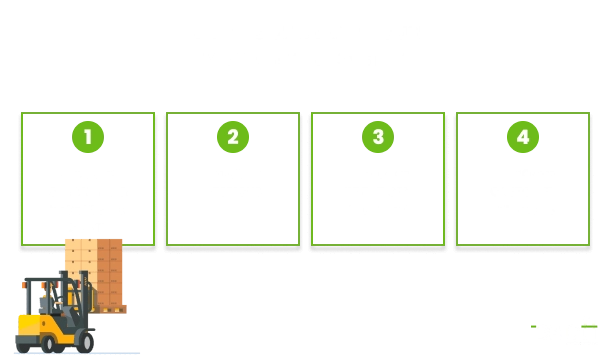
Data-driven decisions
Since you will connect the effective warehouse management systems to your available inventory and sales channels, they must provide real-time operations. Thus, you can define warehouse management issues that can pose a high risk quickly – for example, in the case of warehouse theft or when relevant products or items are damaged during transportation. Also, you can analyze and report on the warehouse employees’ productivity faster, which ensures you know where they spend their work time mostly and what processes to improve.
Faster order fulfillment
In today’s competition within the retail environment, when even same-day delivery is considered the norm, you must have efficient tools to reduce order fulfillment time. Thanks to a WMS integrated with barcode scanners, your staff will operate much faster while picking and packing orders. That allows cutting down processing times and order fulfillment latency.
Reduction in processing costs
If your warehouse team needs less time for picking and packing items and for completing other warehouse processes, you can drastically reduce your processing costs. So you should count current processing costs per order now, and after that, you will see how much ROI you receive thanks to applying a WMS.
Error elimination
A WMS and barcoded inventory help cut down the time required for administration, which, in turn, allows reducing the risk of human errors. With an appropriate warehouse management system, your employees at the warehouse can easily scan product barcodes during various operations. Therefore, the WMS can notify them in the case of scanning wrong products and communicate relevant inventory changes via sales channels in real-time. That also helps reduce the number of frustrated clients and bad customer reviews.
Time-saving
Using barcode scanners for your warehouse management allows saving time when conducting stock takes and enhancing things even further, thanks to cycle counts.
Choosing a warehouse management system
Choosing a warehouse management system depends on the specific features of your warehouse
operations and the goals you intend to achieve. Also, the appropriate warehouse management
system allows increasing efficiency and fulfilling orders more accurately, which means you
can conduct more warehousing procedures at a lower cost.
In addition, an effective warehouse management system wms should serve as a guide that helps
all employees become more productive in warehouse organization. To do that, the right warehouse
management system must provide real-time insights regarding all aspects of your warehouse process
to help employees be more programmatic.
These insights should cover packing and shipping, inventory tracking, order fulfillment, and
even labor and provide easy-to-understand warehouse management statistics that warehouse managers
and staff can use to enhance daily and long-term warehouse management processes. The right
warehouse management system should also provide scalability, which can help your organization
to grow and correspond to changing market conditions.
Below we also provide some critical factors to consider for choosing a warehouse management
system:
ROI
The more warehouse operations you conduct – the greater ROI potential. These operations may include picking and packing, shipping and receiving, or accounting for inbound and outbound goods.
User-friendly UI
Along with advanced functionality available in your warehouse management system wms, it must have a user-friendly UI. That helps warehouse managers and other employees get the maximum out of the particular wms software.
Automation
You should look for a warehouse management solution that supports wireless technologies
and allows automating tedious, repetitive warehouse processes. Thus, you need to opt for
warehouse management software that provides real-time delivery, and warehouse inventory is
updated after the new information is added, with no periodic batch.
Besides, integrating with shipping partners and the accounting software in real-time helps
your back office cut down transcription errors, lowers the need for staff, and enhances access
to data throughout the entire warehouse system.
System capacity
You must ensure that you can update your warehouse technology soon. Such an approach helps avoid the need to buy new wms software within a short time and eliminates the potential loss of the company’s valuable time with experiments regarding warehouse management systems.
Technical support
After applying warehouse management software, you can face some problems that are hard to
solve internally. Thus, you may rely on the support teams of your wms vendors. Learn more
about the provision of after-sales technical support and analyze the policies of
maintaining and upgrading your warehouse management system.
Thus, successful wms vendors can take your warehouse process, along with supply chain management
scm, to a higher level of effectiveness, speed, and order accuracy. That will make your business
more competitive and allow satisfying customer requirements while reducing warehouse operation
costs.